14. Assessment of Test Validity
14.1 The testing laboratory shall assess the validity of tests that have deviations from the procedure. The TMC will assist the laboratory in the determination of calibration test validity, if requested by the laboratory. Use the following guidelines as a basis for determining test validity.
14.2 Average Exhaust Gas NOx Levels - The average NOx level during a test should be within 600 ppm of the overall cumulative calibration test average for the laboratory. The cumulative calibration test average is the average NOx level of the last ten calibration tests. Significantly lower NOx levels could cause a reduction in sludge severity.
14.3 Used Oil Analyses - Interpretation:
14.3.1 Iron and Copper Content - The iron and copper content of the used oil samples can indicate the level of wear that occurs during a test. Increased camshaft, rocker arm, and cylinder bore wear causes the iron content to increase. High levels of iron may also increase sludge severity. The rate of change in iron levels indicates the rate of change of wear levels, although wear tends to be linear throughout the test. Copper levels tend to be relatively stable unless excessively high levels of connecting-rod bearing weight loss are experienced.
14.3.2 Silicon Content - Silicon content indicates the level of contamination of the oil from external sources and silicone-based sealers. Silicone-based sealers are used near the rear crankshaft seal housing to seal the oil pan. Investigate the presence of silicone-based sealers, the cleanliness of engine parts during build-up, the cleanliness of the intake-air, and the cleanliness of containers used for dispensing and sampling the oil if high levels of silicone are experienced.
14.3.3 Fuel Dilution - Fuel dilution indicates the degree to which the crankcase oil has been diluted with fuel. Fuel dilution of the crankcase oil is necessary to achieve adequate test severity. However, excessive fuel dilution may promote increased wear and sludge severity. The reproducibility of fuel dilution tends to be poor. Therefore, fuel dilution levels should only be compared to other results obtained from the same analytical laboratory, using the same analytical equipment and technique. Investigate a higher level of fuel dilution than is normally noted.
14.4 Blowby Flow Rate:
14.4.1 The corrected average blowby flow rate shall fall within the range from 1.75 to 2.25 cfm (0.83 to 1.06 L/s). In addition, the requirements listed in 14.3.2 shall also be met.
14.4.2 Between 48 and 192 h, a maximum of twelve corrected blowby flow rate readings may be greater than 2.25 cfm (1.06 L/s). Between 48 and 192 h, the summation of the deltas (delta = [corrected reading in cfm] - 2.25) of blowby flow rate readings above 2.25 cfm are not to exceed 1.2. No more than 16 of the corrected blowby flow rate readings can be less than 1.75 cfm (0.83 L/s) during the first 192 h. The summation of the deltas (delta = 1.75 - [corrected cfm]) of blowby flow rate readings below 1.75 cfm (0.83 L/s) are not to exceed 1.6 during the first 192 h.
14.5 Intake Manifold Vacuum - Depending upon an individual laboratory, intake manifold vacuum will vary in accordance with the altitude of the laboratory, ambient barometric pressure, and the mechanical efficiency of the engine. Laboratories should investigate intake manifold vacuum readings that are abnormal for their laboratory. Abnormal readings can be due to measurement errors in manifold vacuum, engine build, exhaust back pressure, engine speed, engine load, and air-fuel ratio.
14.6 Fuel Consumption Rate - The fuel consumption rate should not exceed 18 lb/h (8.2 kg/s) at any time during the test.
14.7 Oil Consumption - The final oil level cannot be lower than 12 oz (360 mL) (fluid) during the first 192 h of the test. Use engineering judgment concerning test invalidation if the oil level is lower than 12 oz (360 mL) during the remainder of the test.
14.8 Shutdowns - The number of shutdowns are to be minimized. Under no circumstances is the number of shutdowns to exceed twelve, exclusive of shutdowns for blowby flow rate adjustments and scheduled oil level shutdowns. Length of downtime is to be minimized, and under no circumstances is the total length of downtime to exceed 100 h.
14.9 Deviation Percentage - Calculate the deviation percentage in accordance with the following equation:
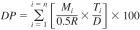
where:
DP = deviation, %,
Mi = magnitude of test-parameter deviation from specification limit at occurrence i,
R = test parameter specification range,
Ti = length of time that test parameter was outside of specification range at occurrence i,
n = number of times that a test parameter deviated from test specification limits, and
D = length of test-phase duration in same units as Ti.
NOTE 12 - Ti is assumed to be no less than the recorded-data-acquisition frequency unless supplemental readings are documented.
14.10 Invalidate any tests exceeding the following deviation percentages:
Primary test parameter: 2.5 %
Secondary test parameter: 5.0 %
14.10.1 Primary Parameters:
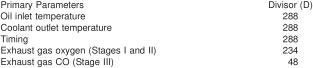
14.10.2 Secondary Parameters:

14.10.3 Special - For tests started prior to September 1, 1992, invalidate the test if the deviation percentage for either engine coolant flow rate or rocker arm cover inlet coolant temperatures exceeds 5.0 %. For tests started on or after September 1, 1992, invalidate the test if the deviation percentage for either parameter exceeds 2.5 %.
14.10.4 Special Parameters:

14.11 Mid Specification Operation - For all tests started on or after September 1, 1992, invalidate the test if the average of steady state operating data for a controlled, primary parameter is offset from the target mean by more than 12.5 % of the allowable control range. For tests started on or after March 30, 1992, list in the test report any parameters that fall outside of these limits.
Example: Temperature specification is 100 +/- 2°
Primary: Average must be within 100 +/- 0.5°
Secondary: Average must be within 100 +/- 1.0°
14.11.1 Primary Parameters:
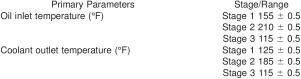
14.11.2 Secondary Parameters:
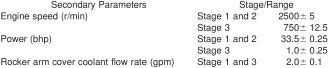
14.12 Stage Transitions - Invalidate any test that does not meet the speed, torque, CO, and O2 values listed in Table 4 during transition from Stage 2 to 3 and Stage 3 to 1.