ASTM D6299 Standard Practice for Applying Statistical Quality Assurance Techniques to Evaluate Analytical Measurement System Performance
1. Scope
1.1 This practice provides information for the design and operation of a program to monitor and control ongoing stability and precision and bias performance of selected analytical measurement systems using a collection of generally accepted statistical quality control (SQC) procedures and tools.
NOTE 1 - A complete list of criteria for selecting measurement systems to which this practice should be applied and for determining the frequency at which it should be applied is beyond the scope of this practice. However, some factors to be considered include (1) frequency of use of the analytical measurement system, (2) criticality of the parameter being measured, (3) system stability and precision performance based on historical data, (4) business economics, and (5) regulatory, contractual, or test method requirements.
1.2 This practice is applicable to stable analytical measurement systems that produce results on a continuous numerical scale.
1.3 This practice is applicable to laboratory test methods.
1.4 This practice is applicable to validated process stream analyzers.
NOTE 2 - For validation of univariate process stream analyzers, see also Practice D3764.
1.5 This practice assumes that the normal (Gaussian) model is adequate for the description and prediction of measurement system behavior when it is in a state of statistical control.
NOTE 3 - For non-Gaussian processes, transformations of test results may permit proper application of these tools. Consult a statistician for further guidance and information.
1.6 This practice does not address statistical techniques for comparing two or more analytical measurement systems applying different analytical techniques or equipment components that purport to measure the same property(s).
2. Referenced Documents
2.1 ASTM Standards:
D3764 Practice for Validation of Process Stream Analyzer Systems
D5191 Test Method for Vapor Pressure of Petroleum Products (Mini Method)
E 177 Practice for Use of the Terms Precision and Bias in ASTM Test Methods
E 178 Practice for Dealing with Outlying Observations
E 456 Terminology Relating to Quality and Statistics
E 691 Practice for Conducting an Interlaboratory Study to Determine the Precision of a Test Method
3. Terminology
3.1 Definitions:
3.1.1 accepted reference value, n - a value that serves as an agreed-upon reference for comparison and that is derived as (1) a theoretical or established value, based on scientific principles, (2) an assigned value, based on experimental work of some national or international organization, such as the U.S. National Institute of Standards and Technology (NIST), or (3) a consensus value, based on collaborative experimental work under the auspices of a scientific or engineering group.
3.1.2 accuracy, n - the closeness of agreement between an observed value and an accepted reference value.
3.1.3 assignable cause, n - a factor that contributes to variation and that is feasible to detect and identify.
3.1.4 bias, n - a systematic error that contributes to the difference between a population mean of the measurements or test results and an accepted reference or true value.
3.1.5 control limits, n - limits on a control chart that are used as criteria for signaling the need for action or for judging whether a set of data does or does not indicate a state of statistical control.
3.1.6 lot, n - a definite quantity of a product or material accumulated under conditions that are considered uniform for sampling purposes.
3.1.7 precision, n - the closeness of agreement between test results obtained under prescribed conditions.
3.1.8 repeatability conditions, n - conditions where mutually independent test results are obtained with the same test method in the same laboratory by the same operator with the same equipment within short intervals of time, using test specimens taken at random from a single sample of material.
3.1.9 reproducibility conditions, n - conditions under which test results are obtained in different laboratories with the same test method, using test specimens taken at random from the same sample of material.
3.2 Definitions of Terms Specific to This Standard:
3.2.1 analytical measurement system, n - a collection of one or more components or subsystems, such as samplers, test equipment, instrumentation, display devices, data handlers, printouts or output transmitters, that is used to determine a quantitative value of a specific property for an unknown sample in accordance with a test method.
3.2.1.1 Discussion - An analytical measurement system may comprise multiple instruments being used for the same test method.
3.2.2 blind submission, n - submission of a check standard or quality control (QC) sample for analysis without revealing the expected value to the person performing the analysis.
3.2.3 check standard, n - in QC testing, a material having an accepted reference value used to determine the accuracy of a measurement system.
3.2.3.1 Discussion - A check standard is preferably a material that is either a certified reference material with traceability to a nationally recognized body or a material that has an accepted reference value established through interlaboratory testing. For some measurement systems, a pure, single component material having known value or a simple gravimetric or volumetric mixture of pure components having calculable value may serve as a check standard. Users should be aware that for measurement systems that show matrix dependencies, accuracy determined from pure compounds or simple mixtures may not be representative of that achieved on actual samples.
3.2.4 common (chance, random) cause, n - for quality assurance programs, one of generally numerous factors, individually of relatively small importance, that contributes to variation, and that is not feasible to detect and identify.
3.2.5 double blind submission, n - submission of a check standard or QC sample for analysis without revealing the check standard or QC sample status and expected value to the person performing the analysis.
3.2.6 expected value, n - for a QC sample analyzed using an in-statistical control measurement system, the estimate of the theoretical limiting value to which the average of results tends when the number of results approaches infinity.
3.2.7 in-statistical-control, adj - a process, analytical measurement system, or function that exhibits variations that can only be attributable to common cause.
3.2.8 proficiency testing, n - determination of a laboratory's testing capability by participation in an interlaboratory cross-check program.
3.2.8.1 Discussion - ASTM Committee D02 conducts proficiency testing among hundreds of laboratories, using a wide variety of petroleum products and lubricants.
3.2.9 quality control (QC) sample, n - for use in quality assurance programs to determine and monitor the precision and stability of a measurement system, a stable and homogeneous material having physical or chemical properties, or both, similar to those of typical samples tested by the analytical measurement system. The material is properly stored to ensure sample integrity, and is available in sufficient quantity for repeated, long term testing.
3.2.10 site precision (R'), n - the value below which the absolute difference between two individual test results obtained under site precision conditions may be expected to occur with a probability of approximately 0.95 (95 %). It is defined as 2.77 times the standard deviation of results obtained under site precision conditions.
3.2.11 site precision conditions, n - conditions under which test results are obtained by one or more operators in a single site location practicing the same test method on a single measurement system which may comprise multiple instruments, using test specimens taken at random from the same sample of material, over an extended period of time spanning at least a 15 day interval.
3.2.11.1 Discussion - Site precision conditions should include all sources of variation that are typically encountered during normal, long term operation of the measurement system. Thus, all operators who are involved in the routine use of the measurement system should contribute results to the site precision determination. If multiple results are obtained within a 24–h period, then it is recommended that the number of results used in site precision calculations be increased to capture the longer term variation in the system.
3.2.12 site precision standard deviation, n - the standard deviation of results obtained under site precision conditions.
3.2.13 validation audit sample, n - a QC sample or check standard used to verify precision and bias estimated from routine quality assurance testing.
3.3 Symbols:
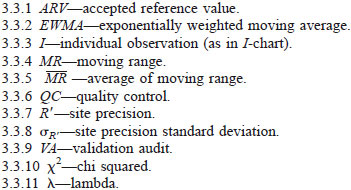