8. Sampling and Specimen Preparation
8.1 Samples shall be taken in accordance with the instructions in Practice D4057, D4177, D5842, or D5854, where appropriate.
8.2 Clean and dry reusable cells before use. Disposable sample cups are not to be reused. Window material usually is 8 µm polyester, 8 µm polycarbonate, or 6 µm polypropylene film. Renewal of the window of the sample cup is essential for the measurement of each sample. Avoid touching the inside of the sample cup, the portion of the window film in the cup, or the instrument window that is exposed to X-rays. Oil from fingerprints can affect the reading when analyzing for low levels of sulfur. Wrinkles in the film will affect the number of sulfur X-rays transmitted. Therefore, the importance of the film's tautness and cleanliness cannot be over stressed. Recalibrate the analyzer when you change the type or thickness of the window film.
8.3 Polyester films often contain impurities that may affect the measurement of low levels of sulfur and may vary from lot to lot. Therefore, if using a polyester film, check the calibration with the start of each new roll.
8.4 X-ray films may vary in thickness from batch to batch. Check the calibration when starting a new roll of any film.
8.5 Samples of high aromatic count may dissolve polyester and polycarbonate films. In these cases, other materials besides these films may be used for X-ray windows, provided that they do not contain any elemental impurities that can adversely affect the results obtained by this test method.
9. Calibration
9.1 Prepare calibration standards by the careful preparation by mass of a 50:50 mixture (based on sulfur content) of the certified thiophene and 2-methylthiophene or n-butyl sulfide with 20 to 80 % mixture of toluene - isooctane or other suitable base material (see 5.1). Exact standards of the nominal sulfur concentrations listed in Table 1 are recommended.
9.2 Preparation of Stock Standard:
Weigh approximately 0.657 g of thiophene and 0.767 g of 2-methylthiophene and record the masses to the nearest 0.1 mg, or weigh 2.286 of n-butyl sulfide to the nearest 0.1 mg. Add the standard materials to a tared 100 mL volumetric flask. Add mixed solvent of 20 % toluene and 80 % isooctane (by volume) or other base material (see 5.1) to a net mass of 50.000 + 0.010 g. This stock standard contains approximately 10 mg/g sulfur. Correct the concentration by multiplying the measured masses by the sulfur equivalency in each of the standards, that is thiophene grams x 0.3803 x purity plus 2-methylthiophene grams x 0.3260 x purity (or n-butyl sulfide grams x 0.2191 x purity) = weight of sulfur in the standard solution. Divide this number by the total mass of the standards and base material added to them, multiply by 1000 mg/g and the result is the actual sulfur concentration in mg/g. This calculation is as follows:
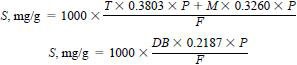
where:
S = final sulfur concentration,
T = mass of thiophene added,
M = mass of 2-methylthiophene added,
DB = mass of di-n-butyl sulfide added,
P = purity of the standard material, and
F = final mass of mixture.
9.3 Preparation of Diluted Standard:
Dilute 25.0 mL of stock standard to 250 mL using the base material. This gives a standard of approximately 1000 mg/kg. Divide the standard concentration calculated in 9.2 by 10 to determine the actual concentration.
9.4 Serial Dilutions:
Prepare serial dilutions of the diluted standard by diluting the following volumes to 100 mL using the base material:
0.5 mL = 5 mg/kg
1.0 mL = 10 mg/kg
5.0 mL = 50 mg/kg
10.0 mL = 100 mg/kg
25.0 mL = 250 mg/kg
50.0 mL = 500 mg/kg
Diluted Standard = 1000 mg/kg
NOTE 3 - Prepare calibrations up to 1000 mg/kg sulfur, and dilute samples with higher concentrations of sulfur to within this concentration range.
9.5 Establish calibration curve data by carefully measuring the net intensity of the emitted sulfur radiation from each of the standards by the procedure described in Sections 10 and 11.
9.6 Construct a calibration model by:
9.6.1 Using the software and algorithms supplied by the instrument manufacturer.
9.6.2 Fitting the data to an equation of the type:
S = aR + b
where:
S = sulfur concentration, mg/kg,
R = net intensity for the sulfur radiation,
a = slope of the calibration curve, and
b = intercept of the calibration curve.
9.6.3 Plotting corrected net intensity in counts per second (cps) versus sulfur concentration. Plot data in two ranges listed in Table 1.
9.7 During collection of calibration data, measure the intensity of the drift monitor standards. Use the intensities from these standards to correct for day to day instrument sensitivity. This value corresponds to A in Eq 5, Section 11. Many instrument manufacturers have built drift correction procedures into their software.
9.8 At the completion of the calibration, measure one or more independent calibration check standards to verify the accuracy of the calibration curve. These standards (see 7.7) are independent of the calibration set. The measured value shall agree with the standard value within +/- 2 % relative or 2 ppm, whichever is greater.
NOTE 4 - NIST traceable gasoline standards are available at the 1, 10, 40, and 300 mg/kg levels. Other concentrations may be prepared by dilution of these standards with a solvent of similar matrix to the standards previously prepared.