6. Apparatus
6.1 Carrier Gas System - Common carrier gases are helium and nitrogen. Paragraph 7.6 provides more details on carrier gases. Means must be provided to measure and control the flow rate of the carrier gas. Any flow or pressure control and measurement combination may be used that will give an accurately known and reproducible flow rate over the desired range.
6.1.1 The main gas supply is regulated with a two-stage regulator which must have a stainless steel diaphragm. Rubber or plastic diaphragms permit oxygen or water to diffuse into the carrier gas. In addition, instruments will have a flow controller between the pressure regulator and column inlet to maintain a constant flow during temperature programming. Copper or stainless steel carrier gas lines, not plastic tubing, should be used to avoid diffusion of oxygen (air) into the carrier gas. When using the thermal conductivity detector, variations in the flow will change retention and response. The carrier gas line pressure must be higher than that required to maintain the column flow at the upper temperature limit for the flow controller to operate properly. A pressure of 40 to 60 psi is usually sufficient.
6.2 Column Temperature Control - Precise column temperature control is mandatory if reproducible analyses are to be obtained. Temperature control must be within 0.1°C if retention times are to be compared with another instrument.
6.2.1 Air Bath -The thermostated forced-air bath is generally accepted as the best practical method of temperature regulation for most applications. Temperatures can be controlled by regulators or proportionally controlled heaters using a thermocouple or platinum-resistance thermometer as a sensing element. The advantage of a forced-air bath is the speed of temperature equilibration. Air bath ovens are readily adaptable to temperature programming and are capable of operating over a range of 35 to 450°C. This range can be extended down to -100°C by using cryogenic equipment.
6.2.2 Other Devices - Liquid baths, drying ovens, incubators, or vapor jacket enclosures are less stable, less convenient means of providing a source of heat to maintain or raise the temperature of a chromatographic column. These devices are not recommended for precision chromatographic applications.
6.3 The Injection Port - The purpose of the injection port is to introduce the sample into the gas chromatographic column by instantaneous volatilization following injection into the gas chromatographic system. Two sample inlet types are in common use in gas chromatography: the flash vaporization and the on-column injection inlets.
6.3.1 The temperature of the flash vaporization inlet should be above the boiling points of the sample components and is limited by the amount of septum bleed generated and the temperature stability of sample components. It should be set at that temperature above which no improvement in peak shape occurs but should be determined by the nature of the sample and the volume injected, not by the temperature of the column. If the inlet temperature is too low, broad peak with a slowly rising front edge will result from slow vaporization of the sample. If the temperature is set far above what is necessary to produce fast vaporization, thermal decomposition of the sample, decreased septum life, and ghost peaks due to septum bleed may be observed. Generally, a good guideline is to maintain the inlet temperature 25 to 30°C higher than the highest boiling point of any sample component.
6.3.2 A glass liner placed inside the injection port will eliminate sample contact with hot metal inner walls of the inlet, which can catalyze thermal decompositions. Any debris left in the liner, especially from biological samples, can be a source of excessive sample adsorption. If a liner is used, the debris can easily be removed by replacing the liner. Deactivation of the glass liner by treatment with dimethyldichlorosilane may be necessary for some compounds.
6.3.3 With on-column injection technique, the sample is deposited in the liquid state directly on the column packing. The sample must be small enough to preclude flooding of the column, with possible detrimental effects to peak shape and column life. Ideally, the on-column inlet is a part of the column, so its temperature may be controlled as the column temperature is controlled. In practice, because an on-column inlet usually has a somewhat higher thermal mass than an equivalent sector of the rest of the column, the inlet must be heated somewhat above the maximum analysis temperature of the column oven. The criteria of good peak shape and quantitation should be used to determine the maximum required temperature for the inlet. One should consider the temperature limit of the column packing when heating the injection inlet and detector. With some samples, a nonheated injection port is adequate, especially with temperature-programmed operation.
6.3.4 Injection Port Septum:
6.3.4.1 The septum is a disc, usually made of silicone rubber, which seals one end of the injection port. It is important to change the septum frequently after two to three dozen injections, or preferably at the end of the working day. The best technique is to change the septum when the column is relatively cool (below 50°C) to avoid contact of stationary phase in a hot column with air (danger of oxidation). After the septum is changed, return the inlet temperature to that which was originally set. The inlet temperature should be the optimum for the particular analysis, as well as within the recommended operating temperature of the septum. If the septum is punctured too many times, it will leak air into the gas chromatographic system, even though it is under pressure. At high temperatures, above 150 to 200°C, air (oxygen) in the carrier gas from a septum leak will degrade the stationary phase. An excessive septum leak will also produce a change incarrier gas flow rate (a change in retention time) and loss of sample (irreproducible peak heights) due to outflow from the leak. When installing the septum, do not overtighten the retaining nut. The septa will swell at high temperature and extrude out of the injection port. A snug fit at room temperature is sufficient. It is important for septum life to make sure the injection needle is sharp with no bent tip. Fine emery cloth, or a fine sharpening stone, can be used to sharpen the point.
6.3.4.2 Ghost peaks may be observed in temperature programmed runs due to septum bleed. Septum bleed is due to the thermal decomposition, 300°C or higher, of the septum that produces primarily lower molecular weight cyclic dimethylsiloxanes. It contributes to baseline response and is frequently observed as evenly spaced peaks in a temperature programmed run in which no sample has been injected. This situation can be demonstrated by the disappearance of ghost peaks after placing aluminum foil (pre-cleaned with solvents such as methylene chloride or toluene) over the inner face of the septum or by turning off the injector temperature and making several blank runs. Septum bleed can be decreased by using either air- or water-cooled septum retaining nuts, by using a septum flush head, or by using special high-temperature septa which are available from a number of gas chromatographic supply houses.
6.4 Detector Temperature Control - The detector temperature should always be above that of the maximum operating analytical temperature, to prevent the possibility of condensation of sample components or stationary phase bleed in the detector and connecting line. Because there is usually some temperature gradient across a detector, the temperature should be set at 30 to 50°C above the maximum analysis temperature to ensure that the entire detector is hot enough to prevent condensation. Usually, it is neither necessary nor desirable to use an excessively high temperature since this can result in reduced sensitivity, increased noise level, frequent need to clean the detector, and thermal decomposition of sample or stationary phase.
6.5 Measurement of Temperature - The choice of sensing elements used to measure temperature depends on the desired accuracy (control about a set point) and precision of the measurements. Instrument read-outs should be verified periodically. Some common temperature measurement devices are as follows:
6.5.1 Standardized Mercury Thermometer:
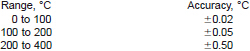
6.5.2 Calibrated Platinum Resistance Thermometer:

6.5.3 Thermocouple (iron - constantan, or other).
6.6 Analytical Column:
6.6.1 The analytical column is a length of tubing (glass, metal, or plastic) that is filled with a packing material. It is discussed thoroughly in Section 7.
6.6.1.1 Column Characteristics - Specified by method.
6.6.1.2 Carrier Gas - Specified by method.
6.6.1.3 Sample Size - Variable within limits.
6.6.1.4 Flow Rates of Carrier Gas and Detector Gases - Variable within limits.
6.6.1.5 Column Temperature - Usually specified by method, and
6.6.1.6 Physical or Chemical Characteristic of Compound Analyzed, or both.
6.6.2 Detector Characteristics - Desirable detector characteristics should include the following:
6.6.2.1 Good stability (low noise level, minimum response to changes in temperature and flow rate).
6.6.2.2 Ruggedness and simplicity.
6.6.2.3 Sensitivity to the components for which analysis is desired. Use either a selective detector for materials of interest or one with a similar response for all components.
6.6.2.4 Linearity of response versus sample concentration. Wide linear range.
6.6.2.5 Rapid response to changes in column effluent composition (small internal volume or flow-through design, or both).
6.6.2.6 Detectors, which are nondestructive and do not contribute to band broadening may be used in series with other detectors.
6.7 Types of Detectors - The detector is located at the outlet end of the chromatographic column and both senses and measures the amount of components that have emerged from the column. The optimum detector should have high sensitivity, low noise level, a wide linearity of response, a response to all compounds of interest, and yet be insensitive to changes in flow and temperature. Selective detectors are characterized as having selective, or greatly enhanced response to certain components. Linearity is decreased for all detectors by column bleed. As many as forty detection systems have been reported, yet only about a dozen are commonly used. Table 1 shows some of the more commonly used detectors. Of these, the thermal conductivity, the flame ionization, the electron capture, the nitrogen-phosphorus, and the flame photometric detectors are the most popular. Nondestructive detectors should be vented to a hood to remove any toxic effluents from the workplace. The effluent from destructive detectors may also be toxic. Details on detectors can be found in the applicable methods in Practices E 516, E 594, E 697, E 840, and E 1140.
6.8 Programmed Temperature Operation - The apparatus used in programmed temperature gas chromatography differs in some respects from that normally used for isothermal work. Basically, the column temperature is varied with time (program rate) to enhance speed of separations. The advantages of using programmed temperature operation include better resolution of lower boiling components because of lower starting temperature and greater sensitivity because of sharper peaks for the higher boiling components.
6.8.1 Column Heater and Temperature Programmer - It is of utmost importance that the column temperature program be reproducible, and that the difference between the set (desired) temperature and the true average column temperature be as small as possible. However, these requirements are difficult to achieve at high heating rates and with columns of large diameter. The mass of the column and its heater should be kept as small as possible. This will minimize thermal lag and will give proportionately small variations around the set temperature at any time. Proportional temperature controllers supply almost full power to the heater until the set point is very closely approached.
6.8.2 The recirculating air bath is the recommended method of heating in programmed temperature gas chromatography (PTGC). The obvious advantages are extremely rapid heating (and cooling after an analysis is completed) with very little temperature lag.
6.8.3 Liquid baths may be used for very low heating rates. They are commonly contained in taped Dewar flasks.
6.8.4 No matter what type of heating device is used, accurate control of the temperature program is necessary. This is usually accomplished by appropriate electronic systems that develop linear (or other) programming rates as desired.
6.8.5 Detectors for programmed temperature gas chromatography should be relatively insensitive to minor temperature and flow fluctuations and insensitive to stationary-phase bleed. These difficulties can be overcome by operating the detector at or near the upper temperature limit for the analysis and by using adequate flow controllers. If stationary-phase bleeding is excessive during PTGC runs, a second conditioning procedure (Section 9) might improve the situation. Alternately, a duplicate analysis column can be used on the reference side of the detector. By equalizing substrate bleed on both sides of the detector, the baseline drift can be substantially compensated. However, this technique does not improve column life and is detrimental to detector linearity. If at all possible, operate the column within its recommended temperature range.
6.8.6 When using the temperature programming technique, the resistance to carrier gas flow in the gas chromatographic column increases with increasing temperature. The flow controllers need a positive pressure of 10 psi to operate properly. By setting the second stage of the regulator to 40 to 60 psi, there will usually be sufficient excess pressure to maintain a constant gas flow through the column. Higher pressures might be required to maintain flow when using relatively long columns of 10 ft, or longer, or packings finer than 120 mesh.
7. Materials
7.1 Stationary Phases - The stationary phases (partitioning agents) that have been successfully used for specific separations are found most quickly by a literature search. Many phases are listed in ASTM publications AMD-25A and AMD-25A-51. The most desirable stationary phases do not volatilize (bleed) significantly from the solid supports at temperatures required to elute the sample.
7.1.1 The polarity of the stationary phases is currently best characterized by McReynolds Constants. The higher the McReynolds Constant, the more polar the phase. Rohrschneider constants can also be used to measure the polarity of stationary phases.
7.1.2 The effects of using polar and nonpolar stationary phases are summarized as follows:
7.1.2.1 Nonpolar stationary phases separate compounds primarily by order of relative volatility or boiling point.
7.1.2.2 Polar stationary phases separate compounds by order of both relative volatility and relative polarity. With polar phases, nonpolar compounds will elute before polar compounds of the same boiling point.
7.1.2.3 Polarity alone is insufficient to describe the separation power of a column. One must consider the overall selectivity of a column towards a set of analytes. This selectivity is a summation of the effects of dispersive interactions, acid-base interactions and the dipole interactions offered by the various pendent groups in the stationary phase.
7.1.3 The stationary phases used in gas chromatographic columns have both minimum and maximum temperature limits. The chromatographer must be aware of the limits for the phase being used. Below the minimum temperature, the phase will behave as either a viscous liquid or a solid. Less efficient separation will be observed, and the chromatographic results will be exhibited as broader peaks in the gas chromatogram due to poor mass transfer of components in the stationary phase.
7.1.3.1 Above the maximum temperature limit, the phase will begin to bleed off the column at an accelerated rate, and the observed results will include a drifting baseline or excessive spiking on the baseline. Under these conditions, the liquid phase will decompose or volatilize, and thus be removed from the column. This situation will eventually lead to decreased retention times with broader peaks resulting in poorer resolution of very close peaks. Peak tailing will also be observed as the uncoated surface becomes exposed by removal of liquid phase, thus shortening column life. Bleeding also can expose bare support surface that can adsorb molecules being analyzed and reduce column efficiency. In extreme cases, phase bleeding will result in fouling the detector and connecting lines. The observed maximum temperature will depend upon many experimental variables, such as type of liquid phase column, conditioning, phase-loading level, column temperature, sensitivity setting of the detector, and purity of the carrier gas. In programmed temperature runs, the column can sometimes be operated for short periods about 25°C above maximum temperature. However, column bleed should be minimized for quantitative results since it decreases the linear range of all detectors.
7.2 Active Solids:
7.2.1 Molecular Sieves - The synthetic zeolite molecular sieve sorbents separate molecules by size and structural shape. Isomers with a more round shape, as branched versus straight chain molecules, diffuse in and out of the zeolite structure more easily than isomers with the long chain structures. Separations are affected by the differences in times required for molecules of different sizes to find their way into and out of the sieve-like structure of the adsorbent. Molecular sieves are most useful for separating H2, O2, N2, CO, and CH4. Carbon molecular sieves are also available, and can be used to separate O2, N2, CO, CO2, H2O, and C1 to C4 hydrocarbons.
7.2.2 Porous Polymers:
7.2.2.1 One type of porous polymer used in gas chromatography is available in the form of microporous cross-linked, polymer beads produced by copolymerizing styrene and divinylbenzene or more polar copolymers, or both. These materials are generally used as received without coating with any liquid phase. They provide symmetrical peaks for polar, hydrogen-bonding compounds such as water, alcohols, free acids, amines, ammonia, hydrogen sulfide, etc., and organic compounds up to molecular weights corresponding to about 170.
7.2.2.2 Another porous polymer is poly(2,6-diphenyl-p-phenylene oxide). This material is useful for the analysis of amines, alcohols, and hydrogen-bonding compounds. It is also used as an adsorbent for trapping trace organic compounds in water and air.
7.2.3 Silica Gel, Alumina, and Carbon - Among the active solid adsorbents are silica gel, alumina, and activated carbon. They are useful for low-boiling hydrocarbons.
7.2.4 Solid adsorbents modified by low concentrations of liquid phases may retain the advantageous properties of both. Some solid adsorbents can be modified by the addition of surface activating compounds such as wetting agents, silver nitrate, and the metal salts of fatty acids.
7.3 Diatomaceous Earth Supports - The most popular gas chromatographic supports are those prepared from diatomaceous earth, also called diatomaceous silica or kieselguhr. The two main types are white and pink in color. The white supports are recommended over the pink supports because of their more inert surface. The former are, however, very friable and must be handled very carefully when preparing packings and loading into gas chromatographic columns. Before using these supports, check the manufacturer's literature for comments on their use.
7.3.1 The white-colored supports are produced by calcination of diatomaceous earth with sodium carbonate as a flux. In this process, the diatomaceous earth fuses, due to formation of a sodium silicate glass. The product is white in color due to conversion of iron oxide into a colorless complex of sodium iron silicate. These white materials are used to prepare the more inert gas chromatographic supports. However, they are fragile and subject to abrasion from excessive handling in the course of sieving, packing, or shipping. Abrasion will produce finer particles, or fines, which will decrease column efficiency.
7.3.2 The pink-colored supports are prepared by crushing diatomaceous earth firebrick that has been calcined with a clay binder. The metal impurities remaining form complex oxides that contribute to the pink color of the support. These pink supports are denser than the white supports because of the greater destruction of the diatomite structure during calcination. They are harder and less friable than the white supports and are capable of holding larger amounts of liquid phase (up to 30 %) without becoming too sticky to flow freely. Their surface is generally more adsorptive than white supports. For this reason, they are not recommended for use in the gas chromatographic analysis of polar compounds. However, pink supports provide excellent efficiencies for the analysis of hydrocarbons and organic compounds of low polarity.
7.3.3 Chemical Treatment of Diatomaceous Earth Supports - Neither the pink nor the white materials give generally acceptable analysis of more polar compounds without further treatment. With these compounds, severe peak tailing is often observed, especially with the dense pink supports. This tailing is due to the presence of adsorptive and catalytic centers on all diatomaceous earth supports. The adsorptive sites are attributed to metal oxides (Fe, Al) and surface silanol groups, -SiOH, on the support surface. The latter are capable of forming hydrogen bonds with polar compounds.
7.3.3.1 Metal impurities are removed by washing with hydrochloric acid, which leaches out iron and aluminum and renders the surface both less adsorptive and less catalytically active. However, even with acid washing, the pink supports are still more adsorptive toward polar compounds than the white-type supports. Acid washing is sometimes followed by base washing, which seems to remove only minor amounts of metal impurities, but is a good pretreatment for supports that are to be used for the analysis of basic compounds.
7.3.3.2 Neither acid or base washing is effective in reducing peak tailing due to hydrogen bonding with the surface silanol groups, -SiOH. These groups are most effectively masked by treatment with dimethyldichlorosilane.
7.3.4 Acid-washed silanized grades of white diatomaceous earths are recommended as supports for nonpolar and medium polarity liquid phases. Because of the hydrophobic character of a silanized diatomaceous earth, even coating of the most polar liquid phases is difficult to achieve. Acid-washed, silanized grades of white diatomaceous earths are recommended as supports for the polar liquid phases, such as polyesters and silicones of high cyano-group content.
7.3.5 If the column is 6 ft (2 m), or less, use particle size of 100 to 120 mesh (125 to 149 µm) for highest efficiency under isothermal conditions. If the column is longer than 6 ft, use 80 to 100 mesh (149 to 177 µm) particles. If temperature programming is used, 80 to 100 mesh particles should be used to lessen resistance to carrier gas flow.
7.3.6 Further information concerning the liquid phase loading is given in 9.3.
7.4 Halocarbon Supports - The two types of halocarbon supports are those prepared from poly(tetrafluoroethylene) and poly(chlorotrifluoroethylene). These supports are relatively inert and are nonpolar. They eliminate peak tailing observed in the analysis of organic compounds capable of hydrogen bonding, such as water, alcohols, amines, etc. They are the preferred supports in the analysis of corrosive halogen compounds such as HF, BCl3, UF6, COCl2, F2, and HCl.
7.4.1 Poly(tetrafluoroethylene) supports require special handling procedures. When used as received, they are soft and tend to form gums upon handling. They can also build up a static charge and spray out of the column during the packing operation. These problems can be virtually eliminated by cooling the support to 0°C before coating with liquid phase and by avoiding the use of glass vessels. Rinsing poly(tetrafluoroethylene) with methanol and drying before use is another way to eliminate the static-charge problem.
7.4.2 Supports prepared from poly(chlorotrifluoroethylene) are structurally harder and are much easier to handle and to pack into a column.
7.5 Tubing Materials - Tubing materials should be chosen on the basis of the following criteria:
7.5.1 They should be nonreactive with the stationary phase, sample solvent, and carrier gas.
7.5.2 They should possess physical properties to withstand temperature and pressure of operating conditions, and
7.5.3 They can be shaped to fit in the column oven of the chromatograph.
7.5.4 Satisfactory materials include glass, nickel, stainless steel, and glass-lined stainless steel. Glass is the material of choice, unless conditions prohibit its use. Nickel tubing is more inert than stainless steel in most applications. Less frequently used column materials are poly(tetrafluoroethylene), aluminum, and copper.
7.6 Carrier Gas - The use of an impure carrier gas will produce problems in gas chromatography. Trace water and oxygen can cause decomposition of the liquid phase coated on the support. The common carrier gases, helium and nitrogen, should contain less than 5 ppm water and less than 1 to 2 ppm oxygen by volume. An oxygen adsorption trap can be used to remove trace oxygen, while trace amounts of water and hydrocarbons with molecular weights higher than methane, can be trapped on a molecular sieve trap. Place the molecular sieve drier nearest the gas supply. Calcium sulfate has been used in drying tubes, but cannot dry carrier gas to the same level as molecular sieve.
7.6.1 For some applications, hydrogen may be the preferred carrier gas. However, additional safety precautions are required due to hydrogen's explosive nature.
7.6.2 Air (oxygen) can leak into the gas chromatographic system through loose fittings or a septum, that has been punctured too many times, even though the carrier gas is under a pressure of 40 to 60 psi. Keep all fittings on the gas delivery lines tight, and check them at periodic intervals. Change the septum in the injection port frequently. Plastic tubing should never be used for carrier gas, hydrogen fuel (for FID), or make-up gas lines due to the possibility of oxygen or moisture diffusing through the tubing wall.
7.6.3 Each cylinder of carrier gas has its own impurity level. Occasional tanks contain large amounts of impurities which might overcome a low-capacity oxygen adsorption trap and destroy a gas chromatographic column at high temperature. A new tank or a fresh oxygen adsorption unit, or both will improve this situation.
7.6.4 Always change the tank when the pressure is less than 200 psi. As the total pressure in the cylinder decreases, there is an increase in the partial pressure of the water and other impurities adsorbed on the inner walls of the gas cylinder. As a result, the last amounts of gas delivered from the gas cylinder contain high levels of impurities.
7.6.5 Carrier Gas for Instruments with Thermal Conductivity Detectors - A major factor in sensitivity is the difference in thermal conductivity of the compound being analyzed and the thermal conductivity of the carrier gas. Helium (thermal conductivity = 33.60 cal/cm-s-°C) is usually the carrier gas of choice.
7.6.6 Carrier Gas for Instruments with Flame Ionization Detectors - The most commonly used carrier gases are nitrogen or helium. A maximum impurity level of 0.05 volume % does not generally interfere with most applications. Hydrogen is less commonly used in the US but is more popular in Europe because of availability and relatively low cost.
NOTE 2 - If hydrogen is used, special precautions must be taken due to its explosive nature, to ensure that the system is free from leaks and that the effluent is properly vented.
7.6.7 Carrier Gas for Instruments with Electron-Capture Detectors - Users should follow the manufacturers' recommendations for the choice of carrier gas. Some common ones are nitrogen or 95 % argon/5 % methane. When using a tritium source in the detector, do not use hydrogen as the carrier gas. Hydrogen will replace tritium in the source.