IEC 60296 Fluids for Electrotechnical Applications - Unused Mineral Insulating Oils for Transformers and Switchgear
6 Properties, their significance and test methods
6.1 Viscosity
Viscosity influences heat transfer and therefore the temperature rise of the equipment. The lower the viscosity, the easier the oil circulates leading to improved heat transfer. At low temperatures, the resulting higher viscosity of oil is a critical factor for the cold start of transformers with poor or no circulation of oil and therefore possible overheating at the hot spots, and negatively influences the speed of moving parts such as in power circuit breakers, switchgear, on-load tap changer mechanisms, pumps and regulators. The viscosity at the lowest cold start energizing temperature (LCSET) shall not exceed 1800 mm2/s (respectively 2500 mm2/s at -40 °C, see Table 1). This lowest cold start energizing temperature (LCSET) for transformer oils is defined in this standard as being -30 °C (this is 5 K lower than indicated in IEC 60076-2). Other LCSET (see Table 1) can be agreed between supplier and purchaser.
Low temperature switchgear oil should have a lower viscosity at LCSET: max. 400 mm2/s. Standard LCSET of low temperature switchgear oil is defined at -40 °C but other LCSET may be agreed between supplier and purchaser.
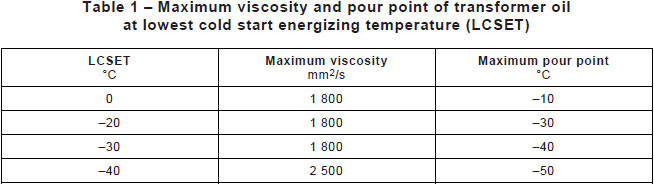
Viscosity shall be measured according to ISO 3104, and viscosity at very low temperatures according to IEC 61868.
6.2 Pour point
The pour point of mineral insulating oil is the lowest temperature at which the oil will just flow. It is recommended that the pour point should be at least 10 K below the lowest cold start energizing temperature (LCSET). If a pour point depressant additive is used, this shall be declared by the supplier to the user. Pour point shall be measured in accordance with ISO 3016.
6.3 Water content
A low water content of mineral insulating oil is necessary to achieve adequate breakdown voltage and low dissipation losses. To avoid separation of free water, unused insulating oil should have limited water content. Before filling the electrical equipment, the oil should be treated to meet the requirements of IEC 60422. Water content shall be measured in accordance with IEC 60814.
6.4 Breakdown voltage
The breakdown voltage of transformer oil indicates its ability to resist electrical stress in electrical equipment. Breakdown voltage shall be measured in accordance with IEC 60156. The supplier shall demonstrate that after treatment to reduce particles, water and dissolved air by a vacuum procedure (see note), the oil shall have a high dielectric strength (breakdown voltage >70 kV).
NOTE This treatment referred to consists of filtration of the oil at 60 °C by vacuum (pressure below 2,5 kPa) through a sintered glass filter (with a maximum pore size of 2,5 µm).
6.5 Dielectric dissipation factor (DDF)
DDF is a measure for dielectric losses within the oil. DDF values above requirements of Table 2 can indicate contamination of the oil by polar contaminants or poor refining quality. DDF shall be measured in accordance with IEC 60247 or IEC 61620 at 90 °C. In case of dispute, IEC 60247 at 90 °C should be used.
NOTE By agreement between parties, DDF can be measured at temperatures other than 90 °C. In such cases the temperature of measurement can be stated in the report.
6.6 Appearance
A visual inspection of insulating oil (oil sample in transmitted light under a thickness of approximately 10 cm and at ambient temperature) will indicate the presence of visible contaminants, free water or suspended matter.
6.7 Acidity
Unused mineral insulating oil should be free from any acidic compound. Acidity shall be measured according to IEC 62021-1 or IEC 62021-2.
6.8 Interfacial tension (IFT)
Low IFT sometimes indicates the presence of polar compounds. IFT shall be measured in accordance with EN 14210 or ASTM D971.
6.9 Sulphur content
Different organo-sulphur compounds are present in mineral oils, dependent on the crude oil origin and the degree and type of refining. Refining reduces the content of sulphur and aromatic hydrocarbons. As some naturally present sulphur compounds have an affinity to metals, they may act as natural oxidation inhibitors or they may promote corrosion.
Sulphur content is a specific requirement of 7.1.
Sulphur content should be measured following IP 373 or ISO 14596.
6.10 Corrosive and potentially corrosive sulphur
Some sulphur compounds, e.g. mercaptans, are very corrosive to metal surfaces, i.e. steel, copper and silver (switchgear contacts) and shall not be present in new oil. This type of corrosive sulphur should be detected following DIN 51353.
Some other sulphur compounds, e.g. dibenzyldisulphide (DBDS), may result in the deposition of copper sulphide (Cu2S) in paper insulation, reducing its electrical insulation properties (see Annex A). This has resulted in several equipment failures in service.
IEC 62535, based on work performed by CIGRE WG A2.32, provides the best currently available method to detect potentially corrosive sulphur compounds in oil. It applies only to oils that do not contain a metal passivator additive (declared or undeclared).
For passivator-containing oils, see Clause A.3.
6.11 Additives (see 3.4)
6.11.1 General
The generic type of all additives shall be declared in product data sheets and certificates of compliance. For antioxidant additives and passivators, their concentrations shall also be stated.
6.11.2 Antioxidant additives (see 3.5)
Antioxidants slow down the oxidation of oil and therefore the formation of degradation products such as oil sludge and acidity. It is useful to know whether and in what proportion antioxidant additives have been added in order to monitor additive depletion during service.
Additives that slow down the oxidation of mineral insulating oils include:
- inhibitors such as phenols and amines (see 3.5.1). The most widely used inhibitors are DBPC and DBP (see 3.5.1). Detection and measurement of DBPC and DBP shall be carried out in accordance with IEC 60666. IEC test methods are not available for other types of inhibitors.
- other antioxidant additives such as sulphur- and phosphor- containing compounds, e.g. organic polysulfides and dithiophosphates (see 3.5.2). An antioxidant additive of this type is DBDS (see 6.10), but it is not accepted as it is known to be corrosive to copper and will likely result in the oil failing the potentially corrosive sulphur test of IEC 62535. IEC test methods are in preparation only for DBDS (see 6.21) and not for the other antioxidant additives of this type.
- metal passivators (see 6.11.3).
6.11.3 Metal passivators
Some of these additives form thin films on copper, preventing the catalytic effect of copper in oil and the formation of harmful copper sulphide deposits in paper by reaction with corrosive sulphur compounds contained in the oil. Some of them protect the oil from the catalytic action of metals and slow down the rate of oxidation of oil. Passivators therefore slow down the oxidation process in IEC 61125 as they passivate the surface of the catalysing copper-wire, thus leading to an optimistic result of the oxidation stability test. Some of them are also used to reduce the electrostatic charging tendency of oils (see 6.14).
Three main types of benzotriazole derivatives are typically used as metal passivator additives: N-bis(2-Ethylhexyl)-aminomethyl-tolutriazole (TTAA), benzotriazole (BTA) and 5-methyl-1H-benzotriazole (TTA). Detection and measurement of these additives shall be according to IEC 60666.
Several other compounds can be used as metal passivator additives, such as N,N-bis(2-ethylhexyl)-1H-1,2,4-triazole-1 methanamine (TAA), diamino-diphenyldisulphide, nicotinic acid, hydroquinoline and other sulphur-based compounds, for which no IEC test methods are available.
6.11.4 Pour point depressants
These additives are used to improve the viscosity and pour point of oils at very low temperatures. Detection and measurement of the two main types of pour point depressant additives used (polynaphthalenes and polymethacrylates) shall be according to IEC 60666.
6.12 Oxidation stability
Oxidation of oil gives rise to acidity and sludge formation. This can be reduced by using oils with a high oxidation stability leading to longer service life time by minimizing sludge deposition and maximizing insulation life. Oxidation stability is measured in accordance with Method C of IEC 61125:1992. There is an option for stricter limits for special applications. In some countries more stringent limits and/or additional requirements and tests may be requested.
Test durations for oils containing inhibitors shall be as indicated in Table 2. Test duration for oils containing other antioxidant additives and metal passivators shall be 500 h.
Passivator-containing oils shall be tested for oxidation stability before the passivator additive has been added to the oil (when possible), using the test durations of Table 2.
6.13 Gassing tendency
Gassing tendency of mineral insulating oil, i.e. the gas absorbing property of oil when subjected to corona partial discharges, is only necessary and important for special equipment like HV (high voltage) instrument transformers and bushings. It is a measure of the rate of absorption or evolution of gas into oil under prescribed laboratory conditions. Gas absorption properties could be related to oil aromatic content. Gassing tendency is measured using Method A of IEC 60628:1985.
Gassing tendency testing is a specific requirement of 7.3.
NOTE Additives such as 1,2,3,4- tetrahydronaphtalene (tetralin), mono or dibenzyltoluene and others have been proposed to reduce the gassing tendency of some oils, but are not described in IEC 60666. Mono and dibenzyltoluene are described in IEC 60867.
6.14 Electrostatic charging tendency (ECT)
ECT of oil is an important property for certain designs of HV and EHV transformers which have oil pumping rates that can give rise to the build-up of electrostatic charge. This charge can result in energy discharge causing transformer failure.
ECT testing is a specific requirement of 7.2.
NOTE A method to measure ECT is proposed by CIGRE Technical Brochure 170. ECT can be reduced by using metal passivator additives such as BTA and TTA.
6.15 Flash point
The safe operation of electrical equipment requires an adequately high flash point that is measured in accordance with ISO 2719 (Pensky-Martens closed cup procedure).
6.16 Density
In cold climates, density of oil shall be low enough to avoid the ice that results from the freezing of free water to float to the oil surface and possibly lead to fault conditions developing such as flashover of conductors. Density shall be measured in accordance with ISO 3675 (reference method) but ISO 12185 as well is accepted.
6.17 Polycyclic aromatic content (PCAs)
Some PCAs are classified to be carcinogens and therefore need to be controlled to an acceptable level in mineral insulating oil. The total amount of PCAs can be measured by extraction with DMSO (dimethylsulfoxide) under the conditions of IP 346.
NOTE Acceptable limits of total or individual PCAs are specified in national and local regulations.
6.18 Polychlorinated biphenyl content (PCBs)
Unused mineral insulating oil shall be free from PCBs. The reference test method is IEC 61619.
NOTE Acceptable limits of total or individual PCBs are specified in national and local regulations. Further European specifications are described in Directive 96/59/EC.
6.19 2-Furfural (2-FAL) and related compounds content 2-FAL and related compounds in unused mineral insulating oils can result either from improper re-distillation after solvent extraction during refining or from contamination with used oil.
Unused mineral insulating oils should have a low level of 2-FAL and related compounds; measurement should be carried out according to IEC 61198.
NOTE "Related compounds" are: 5-hydroxymethyl-2-furfural (5HMF), 2-furfurylalcohol (2FOL), 2-acetylfuran (2ACF) and 5-methyl-2-furfural (5MEF).
6.20 Particle content
Particles in unused mineral insulating oil may result from manufacturing, storage or handling of the oil, and may affect its breakdown voltage (see 6.4). Measurement should be carried out according to IEC 60970.
6.21 DBDS content
This compound is corrosive at normal transformer operating temperatures and can produce copper sulphide. It therefore shall not be present in unused oil (see 6.10). For the test method for measuring DBDS, see IEC 62697-1 (in preparation).
6.22 Stray gassing of oil
Some oils can produce gases such as hydrogen, hydrocarbons and carbon oxides at low temperatures (< 120 °C) without thermal or electrical faults in a transformer, sometimes even without operational stress. This phenomenon could result in a high production of gases and a misinterpretation of DGA results.
NOTE Methods to measure stray gassing are described in CIGRE Brochure 296 and ASTM D7150. Inhibited grades typically produce less stray gassing than uninhibited ones.
7 Specific requirements for special applications
7.1 Higher oxidation stability and low sulphur content
For transformers with higher operating temperatures or designed for extended service life, there may exist restricted limits after oxidation test (see IEC 61125:1992, Method C). Mostly, such oil is inhibited.
- Total acidity: max. 0,3 mg KOH/g;
- Sludge: max. 0,05 %;
- DDF at 90 °C: max. 0,050;
- Total sulphur content: max. 0,05 % (before oxidation test).
7.2 Electrostatic charging tendency (ECT)
For equipment with high oil circulation speed (OF- or OD-cooled power transformers (IEC 60076-2)), as e.g. HV/DC transformers, a limit may be agreed between purchaser and manufacturer.
7.3 Gassing tendency
For equipment with high electrical field stress or special design, gases formed when subjected to corona partial discharges (6.13) shall be absorbed by the oil. Therefore the gassing tendency according to IEC 60628 shall be agreed upon between the supplier and purchaser of the oil for such equipment.
NOTE In Poland, a gassing tendency ≤ +5mm 3 /min is used for equipment ≥ 400 kV.
Annex A
(informative)
Potentially corrosive sulphur
A.1 Mechanism of copper sulphide deposition
The mechanism of copper sulphide (Cu 2 S) deposition is still not fully elucidated, but it may involve dissolution and transport of copper by sulphur containing species forming complexes with copper. These complexes can then be absorbed by cellulosic insulation where they decompose into Cu2S.
The strong influence of temperature and oxygen on this process indicates that some oxidized sulphur species may be more active than those originally present in oil, or that other oxidation products are important as co-complexing agents (see CIGRE Technical Brochure 378). Cu2S deposition occurs preferentially in equipment where corrosive sulphur compounds are present in oil, unvarnished or unprotected copper is used, operating temperatures are high and the amount of oxygen in oil is limited. The optimal oxygen content for copper transport seems to be relatively low, probably in the region of a few thousand ul/l, but deposition may occur over a wide range of oxygen contents.
A.2 Corrosive sulphur compounds in oil
Although many sulphur compounds are known to be corrosive for copper, few have been identified as components of insulating oil. The only compound shown so far to be a potent Cu2S forming agent and to be present in significant amounts in transformer oil is dibenzyl disulfide (DBDS). Most oils found to be forming Cu2S contain this substance. However, refining processes using severe hydrotreatment can easily remove this reactive compound from oil. Several other substances (including disulphides, thioethers, various oxidized sulphur compounds and elemental sulphur) have been shown to cause Cu2S formation in the IEC 62535 test, when added to originally non-corrosive oils.
A.3 Detection of corrosive sulphur compounds in passivator-containing oils
When oil in a transformer contains a metal passivator additive, a thin protective layer of passivator is formed on copper surfaces, preventing copper from dissolving in oil, reacting with corrosive sulphur compounds present in oil, and depositing in paper insulation as harmful copper sulphide (Cu2S).
The same occurs when testing passivator-containing oils according to IEC 62535. This test method therefore cannot detect corrosive sulphur compounds present in passivating oils and may provide "false negative" results for such oils. Passivator-containing oils testing negative as new oils may then test positive and start depositing harmful Cu2S after the additive has been consumed by aging in transformers service.
In order to detect corrosive sulphur compounds in oil containing a metal passivator additive (declared or suspected), the passivator additive has to be removed first from the oil. The two following procedures can be used for that purpose. Both are intended for newly available types of oils only, not for normal deliveries of oil.
Procedure 1
In this procedure, metal passivator additives are eliminated by specific adsorption from the oil:
a) stir 100 ml of passivator-containing oil with 500 mg of Chromabond HR-XC adsorbent (a strong, mixed-mode, polymer-based cation exchanger for basic analytes), for 1 h, then filter out the adsorbent; or
b) extract 60 ml of oil under a slight vacuum on a 3 ml column containing 200 mg of the adsorbent, if the initial concentration of passivator was < 200 mg/kg.
Procedure 2
This procedure is based on the observation that metal passivator additives in oil are consumed by oxidation aging (in accelerated tests in the laboratory and in transformers in service):
a) Run the passivator-containing oil in the test cell used in Method C of IEC 61125:1992 at 120 °C for 164 h with an air flow of 0,15 l/h to ensure that the passivator has been consumed by oxidation.
b) Test the aged oil for corrosive sulphur in the test cell of IEC 62535 with new paper wrapped conductor.
c) To avoid false positives with the aged oil (i.e. where oxidation aging compounds of oil are mistakenly interpreted as Cu2S), confirm Cu2S deposition with SEM/EDX or other techniques (according to Annex B of IEC 62535:2008). False positives can also be avoided by carrying out a second IEC 62535 test without copper strip and with paper only, and comparing the appearance of papers after both tests with and without copper.
NOTE 1 The protective layer of passivator on copper has been observed to remain on copper after aging tests in the laboratory, but there is little knowledge on whether and how long it will remain on copper in transformers in service.
NOTE 2 As a complement to IEC 62535 and procedures 1 and 2 for passivator-containing oils, the quantification of corrosive sulphur compounds in oil (e.g., dibenzyldisulphide (DBDS) and total disulphide) can be used to ensure that none of these potentially harmful compounds are present in oil.
A.4 Contamination of oils
Mineral insulating oils suspected of having been accidentally contaminated with silicone oils, phthalates or other surface-active chemicals or oils should not be introduced in transformers, since these compounds can produce foaming in oil when trying to degas the transformer, thus making it difficult or impossible to fully degas the transformer oil. The foaming tendency test of ISO 6247 can be used to detect such a contamination.